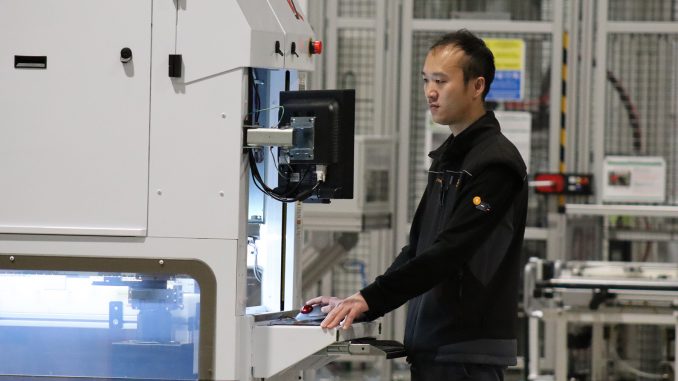
Inseto, a leading technical distributor of equipment and materials, has supplied and installed a Kulicke & Soffa (K&S) Asterion EV hybrid wedge bonder at the UK Battery Industrialisation Centre (UKBIC).
The Asterion EV gives the national battery manufacturing development facility, UKBIC, the ability to provide a wider range of welding technologies to its customers. The new bonder – specially created to support battery module manufacturing – complements the facility’s existing laser welding capability, meaning the facility can now offer different welding technologies dependent on the application.
Andrew Britton, UKBIC’s Business Development Manager, said: “We’re delighted to be collaborating with Inseto on the installation of this new bonder at UKBIC, meaning that we can offer more welding choice to our customers. The bonder also features a non-destructive inline pull test capability to check weld quality. Also, with wirebonding, cells can be reworked and recycled more easily at end of life.”
Matt Brown, Managing Director of Inseto, added: “We’re delighted to be collaborating with UKBIC so that they can offer wirebonding as a means of interconnecting the many cells in a battery pack. Laser welding and ultrasonic wirebonding processes both have roles to play in battery pack manufacturing, but it’s the latter’s ability to place suitably sized wires that can act as individual fuses for each and every cell that’s got people interested. Also, there’s no need to pre-form complex busbars, which is the case for laser welding.”
The K&S Asterion EV, one of the most advanced bonders in the battery sector, is ultrasonic and uses ambient temperature ‘friction welding.’ It can place and bond aluminium wire in the 100 to 600µm diameter range and copper wire in the 100 to 500µm diameter range.
MAIN ENDS
The UK Battery Industrialisation Centre (UKBIC) offers and develops wirebonding using a K&S Asterion EV wedge bonder, supplied and installed by Inseto.
NOTES TO EDITORS
This press release was issued on behalf of Inseto (UK) Limited by technical content creation and communications agency DECLARATION (www.declaration.co.uk, +44 (0)1522 789000).
If you have any editorial enquiries in relation to this announcement, please contact Mandy Warrilow, Press Officer, mandy@declaration.co.uk. Please contact Richard Warrilow, Technical Author, richard@declaration.co.uk, if you require an article or any other form of copy in relation to this press release.
Please contact Matt Brown on +44 (0)1264 334505 or via email (matt.brown@inseto.co.uk) in relation to all advertising and sponsorship matters.
Please contact Richard Robinson, PR & Communications Manager (richard.robinson@ukbic.co.uk) for details about UKBIC.
About Inseto (UK) Limited
Established in 1987 and ISO 9001:2015 Certified since 2005, Inseto is a leading technical distributor of equipment and related materials to the semiconductor, microelectronic & advanced technology sectors, as well as adhesives for electronics, automotive and industrial manufacturing.
The company has three divisions, namely:
- Equipment Division, which provides manufacturing equipment for the Microelectronic, Photonic, Electronic, Photovoltaic and Semiconductor industries etc.
- Consumable Division, which provides assembly materials and machine consumable items for the Semiconductor, Electronic, Microelectronic, Photonic MEMS and Hybrid assembly industries etc.
- Adhesive Division, which provides technically advanced adhesives for bonding, sealing and encapsulation, and which exclusively represents DELO Industrial Adhesives in the UK and Ireland.
Inseto is based in Andover in a high-tech building that houses an adhesives application laboratory, demonstration areas for equipment and instrumentation, and training rooms.
Customer support is at the heart of Inseto’s Total Customer Service philosophy, where the company aims to understand, communicate and fulfil the needs of its customers. The company is committed to meeting customer requirements through the application of high standards of quality and customer care (both before and after sales) by continually investing in training and adopting a policy of continuous improvement.
For further information please visit www.inseto.co.uk
About UKBIC
The £130 million UK Battery Industrialisation Centre (UKBIC) battery manufacturing development centre was opened by the Prime Minister in July 2021. The unique national facility provides the missing link between battery technology, which has proved promising at laboratory or prototype scale, and successful mass production. Based in Coventry, UKBIC welcomes manufacturers, entrepreneurs, researchers and educators, and can be accessed by any organisation with existing or new battery technology – if that technology brings green jobs and prosperity to the UK.
In addition to funding from the Faraday Battery Challenge through UK Research and Innovation, UKBIC is part-funded through the West Midlands Combined Authority. The facility was delivered through a consortium of Coventry City Council, Coventry and Warwickshire Local Enterprise Partnership and WMG, at the University of Warwick, following a competition in 2018 led by the Advanced Propulsion Centre with support from Innovate UK.
For further information please visit www.ukbic.co.uk